Demcon develops, produces and tests complete system in the Netherlands within one month
Technology developer and producer Demcon delivered its first batch of ventilation systems. Within the space of one month, Demcon succeeded in developing, producing and testing a complete ventilation system in the Netherlands that is suitable for the respiration of coronavirus patients in intensive care. The Ministry of Health, Welfare and Sport will distribute the system among the nation’s hospitals. Soon, Demcon will supply a total of 500 ventilation systems. “The government took a leap of faith in placing an order for 500 systems with us, because although we already have a lot of knowledge of and experience with ventilation technology and modules, we have never supplied a complete ventilation system before,” says Demcon CEO Schipper. “Our employees have lived up to that trust, with every possible effort, sometimes working day and night. I am pleased that we can contribute to the great challenge of this moment – the optimal treatment of patients. This use of technological knowledge to solve social issues is in our DNA.”
The DemcAir ventilation system is based on the unique ventilation technology that Demcon macawi respiratory systems has developed for use in the treatment of every patient, from preterm to adult. The individual ventilation modules have been in production at Demcon for many years, but until now, Demcon was supplying these modules to manufacturers of respiratory systems in Germany, the US, Mexico, China and Japan. Demand from China had already increased strongly at the end of January, and now production has been scaled up considerably. Various measures have been taken to facilitate this: the expansion of the number of production lines, more intensive collaboration with suppliers, and the training of production employees, from Demcon and fellow companies.
Fully-fledged ventilation system
In addition to these modules, Demcon has now developed a fully-fledged ventilation system, in the Netherlands, for the treatment of (young) adults. Demcon started preparations on Thursday, 19 March, and on Sunday, 22 March, the ministry ordered 500 systems to be delivered. After successful clinical testing on several patients, the first units have now been delivered – within one month.
Medical product development
That one-month period is exceptionally short, says CEO Dennis Schipper. “Even though we had the ventilation module available and we built the complete system as simply as possible, it is and will remain complex. Such a ventilation system is vital for ICU care, must be 100% safe for the patient and easy to operate by doctors and nurses. We have therefore paid a lot of attention to its safety and ease of operation, and have tested it carefully. In doing so, we were able to build on the experience that we have gained over the past ten years with medical product development in projects that usually last many months to several years. In particular, our expertise in quality assurance and experience in certifying medical products were now crucial.”
National expert group
Speed and care must continue to go hand in hand, agrees Lieke Poot, clinical physicist at the Isala hospitals in the Zwolle region and president of the Dutch Association for Clinical Physics. Clinical physicists are responsible for the reliability and safety of medical equipment in hospitals. On behalf of the Federation of Medical Specialists, Poot is a member of the national expert group for respiratory equipment at the Ministry of Health, Welfare and Sport (VWS). “The expert group lists which devices from outside hospitals are suitable for intensive care, assesses offers from existing suppliers and guides manufacturing initiatives. A lot of smart people and companies want to help and come up with inventive ideas. It’s nice to observe that everyone is in solution mode. This is life-supporting equipment, so as an expert group we have to see whether something works well and contributes to patient treatment.” In that respect Demcon has a big lead, according to Poot. “They have a lot of experience with the mechanical part, the ventilation module that has been used in practice for years. We were confident that they could build a housing and software around it in a short time; that’s why we advised VWS to order 500 systems.”
Pressure cooker procedure
A manufacturing process for a medical device, including clinical tests and certification, can normally take up to a year or more, Poot explains. “Now we are following a kind of pressure cooker procedure, in which we cannot fully follow the applicable laws and regulations, yet we have to arrive at a safe and functional product. We developed this procedure gradually, in an intensive collaboration with Demcon. We are mutually very transparent and at our request they have had Dekra (the notified body, ed.) take part in the preparation of the technical documentation and risk management. As a result, some sort of certification has already taken place, while usually the documentation only goes to Dekra when a design has been completed. Everyone acknowledges the importance of speed, so we can realise things that normally cannot be realised in such a short time. We also asked Demcon to conduct the clinical tests in three hospitals, of course with the consent of the patients. This allowed people from different angles and with different protocols to participate in the tests. That broader view of end users is necessary, particularly now; they have to confirm whether a product can be used clinically.”
Intensive collaborations
The DemcAir ventilation system was created thanks to intensive collaborations, Schipper emphasises. “Firstly, within our company between numerous colleagues spread over different locations.” The same applies, as Poot declares, to Demcon’s close collaboration with the government as its commissioner. Schipper says, “Communication lines are short; we can consult quickly with the people of the National Consortium for Resources [Landelijk Consortium Hulpmiddelen] and the expert group at the ministry.” Poot adds, “Everyone puts their shoulders to the wheel; there is trust and openness towards each other. Normally, a company like Demcon would think more about the confidentiality of its documentation. This is not possible at this stage, because of the speed. That sharing of information is very nice.” In addition, a large number of partners have contributed to the realisation of the DemcAir. From the medical side, these are the Erasmus Medical Centre in Rotterdam, the Isala in Zwolle and the Catharina Hospital in Eindhoven.
Industrial partners
Suppliers must ensure the timely delivery of the essential components and submodules – the complete system, including the central module, contains over 200 different components. “We obtain them from a large number of suppliers. Together with our project buyers, the suppliers have used all possible creativity to ensure an adequate supply. Here I would like to mention especially Allied Motion, SPIE, VDL, 2E Interconnection, Hoerbiger, tbp electronics and CE Persluchttechniek. Dekra’s test knowledge is also indispensable. Our thanks go to all of our forty-plus partners. The support we have received from other companies and individuals is also heart-warming.”
About Demcon
Demcon (700 employees) develops, produces and supplies technology and innovative products. The Demcon group has locations in Best, Enschede, Delft, Groningen, Münster (Germany) and Singapore. The company was born out of the founders’ passion for combining creativity and technical skills aimed at solving complex issues. These issues are of a technological and social nature, and often have a direct or indirect impact on people and their living environment. Whether medical solutions, sustainable innovations for themes such as water and energy, or systems that guard our safety, Demcon contributes – for current and future generations. In addition to developing technical solutions, Demcon is committed to stimulating entrepreneurship and investing in talent and education.
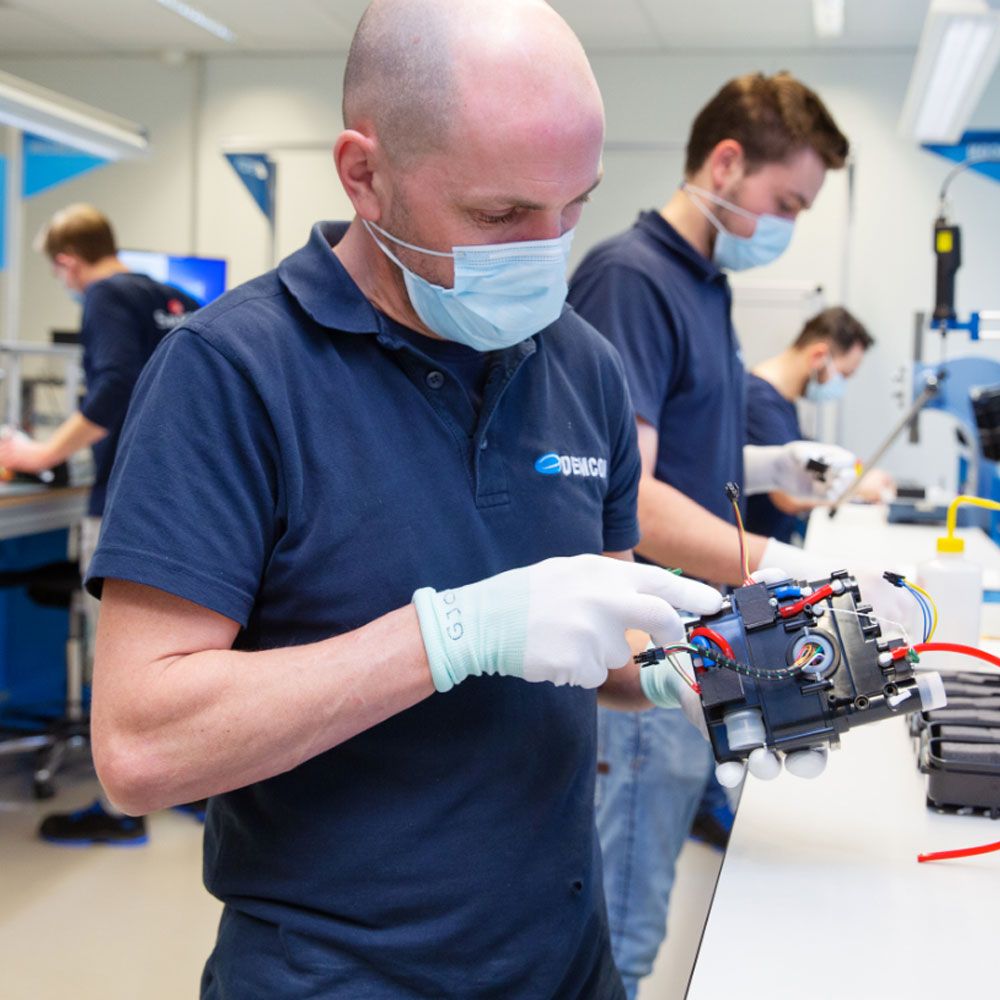